この研究を終えると、先生はマイクロマシンの研究にのめり込んでいった。九州工業大学に情報工学部が設立されたのを機会に助教授として移ることになった。文部省のパイロットプランで設立された学部で、アメリカの大学に似て雑用も少なく、研究に専念できる環境が気に入った。そして、九州工業大学で始めたのが「マイクロ光造形法」だった。
「ある展示会で、光造形法という技術に出会ったんです。これは光(紫外線)を受けると固まる性質のある光硬化ポリマーを利用して、造形物をつくるというものです。カメラのモックアップモデルとか工業製品をつくる金型などに利用されていたものなんですが、ものを削って造形するのではなく、光でポリマーを固めて立体をつくるなんて面白いなと魅力を感じたんです。カメラのモデルとか金型とかは大きなものだけれど、これをミクロサイズでできないかとひらめいたわけ」
当時、マイクロマシンの研究は、半導体を使った「シリコンプロセス」といわれるものが中心で、これでマイクロマシンをつくるとなると、億単位の予算が必要になる。ところが、この光造形法なら、レーザーで細い線でやればすぐできると思ったのだそうだ。
「ところが、新人研究者のぼくの研究室には300万円するレーザーを買うお金なんてなかった(笑)。まあ、それでも紫外線で固まる樹脂だから何とか工夫すればできるだろうということで考え付いたのが、細かい原理は省略するけれど、光学顕微鏡を改造して利用する方法。ところが、その顕微鏡だって250万円もする! そこで、他の研究室の先生に頼んで、使っていない顕微鏡を借りたんです。研究室にいた4年生の広渡君と、これ分解しちゃうぞといって、二人で40万円もする対物レンズなんかもばらしてしまった。貸してくれた先生は、ご自分の顕微鏡がバラバラに分解されたなんて夢にも思っていなかったでしょう(笑)。でも、今でもその先生には感謝していますよ。私も優秀な若手研究者のサポートに熱心なのは、その先生の影響ですね」
生田先生たちは、その顕微鏡を使って、紫外線ビームをつくることにチャレンジした。覗く側から光をあてれば光が絞れる。レーザーのかわりのキセノンランプを使って、必要のない波長の光はカットして、紫外線を通さないプラスチックの真ん中に穴をあけ、5マイクロメートルのビームをつくったのである。
「ところが、霧の中に光をあてるとにじむように、ポリマーを固める部分がにじんでしまって50マイクロメートルの大きさになってしまった。マイクロの領域だと光が散乱してしまうんですね。なにしろ世界で最初の挑戦だから、だれにもアドバイスを受けることができないわけ。ポリマーの専門家もわからない。ポリマーに何かの材料を混ぜると散乱しないことだけはわかったので、100種類もの材料で試したりしたんです。広渡君は、実験が大好きな学生で、あれこれ試して最適な材料を探し出してくれました」
こうした研究で生田研究室が自慢できるのは、研究に必要な材料や部品などを外注せずに自分のところでつくってしまうことだという。
「外注するとお金はかかるし、ちょっと不都合が生じたときなど、直して戻ってくるのに半年もかかることがあるんです。でも自分たちでつくれば一晩で直すこともできる。それに研究の基本をしっかり身につけることもできるというプラス面があるんです」
1年後には、マイクロメートルオーダーの3次元の造形物を生みだすことに成功した。世界に発表した論文では、この方法を「IHプロセス(Integrated Harden Polymer Process=集積硬化ポリマープロセス)」と名づけた。
「実を言うと、このIHプロセスという名前は、生田の頭文字のIと広渡君のHから名づけたもの(笑)。頑張ってくれた広渡君の功績を残したかったからね。それから10年経ってアメリカの教科書ではIH=生田・広瀬と載せてくれたよ(笑)」
光造形法の原理
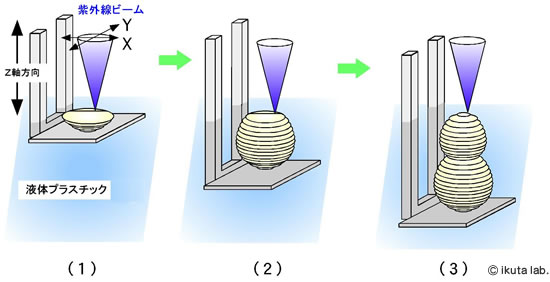